|
Site-Info: Editorial > Ride Insights >
Coaster Basics > Nullebenefertigung - Die "Virtuelle Realität" wird im
Hause Mack Rides real |
|
|
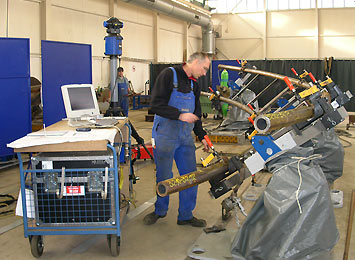 |
Auf dem Arbeitsplatz der Nullebene bei
Mack Rides werden die Schienenrohre und Querriegel eingemessen |
Beim Achterbahnbau spielt Qualität eine große
Rolle, vor allem in der Schienenfertigung. Die Schiene gilt als Herzstück
jeder Achterbahn. Von ihrer Auslegung und anschließenden
Fertigungsqualität hängt es ab, ob der Zug über die Strecke
gleitet oder spürbar unruhig über die Stahlrohre rumpelt.
Qualität hat jedoch in der Schienenfertigung nach der herkömmlichen,
äußerst handwerklich orientierten Methode ihren Preis: Zeit und
Geld. In Zeiten von kostenbewussten Just-in-time-Auslieferungen ein schwieriges
Unterfangen.
Eine mögliche Lösung stellt ein grundlegend
optimiertes Schienenfertigungsverfahren dar. Das Traditionsunternehmen Mack
Rides aus Waldkirch im Schwarzwald hat ein solches Ende 2004 zur
Serienreife gebracht. Durch den Einzug des Computers in den eigentlichen
Fertigungsprozess entsteht eine parallele virtuelle Realität, welche ein
Abbild der Schiene im Rechner vorgibt, die in der Werkhalle praktisch nur noch
nachgebaut werden muss. Diese besondere Schnittstelle zwischen Mensch und
Maschine garantiert, dass jede Abweichung vom Soll in der Fertigung sofort
sichtbar wird, ohne dass die Fertigungsdaten vom Anwender aufwendig
kontrolliert werden müssen. Damit erzielt die Mack'sche
Nullebenenfertigung in kürzester Fertigungszeit eine hohe
Schienenqualität.
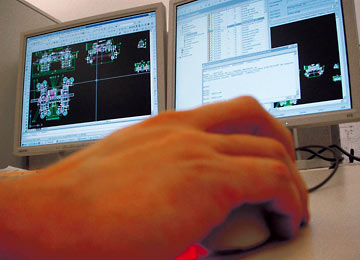 |
Der Computer beherrscht die
Konstruktion |
Eine Achterbahnfahrt lebt von ihren Beschleunigungswechseln,
ob in vertikaler oder lateraler Richtung. Je extremer die Wechsel, desto
genauer ist die Schiene auszulegen. Heute übernehmen ausgeklügelte
Rechen-Algorithmen einen Großteil der Konstruktionsarbeit: Am Computer
entsteht ein dreidimensionales Abbild der Achterbahn. Mittels Raumkurve und Herzlinie wird die Fahrt konsequent optimiert. Eines ist
dabei grundsätzlich zu beachten: Die Beschleunigungswechsel dürfen
nicht zu ruckartig auftreten, sonst empfindet der Fahrgast mitunter unangenehme
Stöße.
Die Aufgabe, eine dreidimensionale Schienenkurve bis zur
Perfektion im Modell zu optimieren, wird von den Achterbahnbauern und externen
Konstruktionsbüros heutzutage sehr gut beherrscht. Das
Ingenieurbüro Stengel aus München hat es vorgemacht und
liefert für Hersteller wie Gerstlauer, Zierer oder
Premier Rides genaue Konstruktionsdaten. Andere Hersteller wie Maurer
Söhne oder Vekoma Rides Manufacturing setzen auf hauseigene,
rechnergestütze Konstruktionstools und stehen dieser Entwicklung in nichts
nach.
Doch letztendlich ist die Qualität der
Schienenfertigung der entscheidende Schlüssel für die Laufruhe einer
Achterbahn. Selbst wenn die Schiene im virtuellen Modell perfektioniert wurde,
kann eine geringere Fertigungsqualität die Fahreigenschaften
verschlechtern. Jeder Hersteller besitzt in Sachen Schienenfertigung ein
eigenes, ständig weiterentwickeltes Know How und lässt sich ungern in
die Karten schauen. Die Produktion von stählernen Achterbahnschienen kann
letztendlich als eigenes Handwerk angesehen werden. Es gehört ziemlich
viel Fingerspitzengefühl dazu, im Fertigungsprozess die Vorgaben des
hochpräzisen, virtuellen Computermodells der Schiene abzubilden. Ein zehn
Meter langes, dreidimensional gebogenes Schienenrohr besitzt im Computermodell
500 und mehr Stützpunkte im Raum, und die gilt es in der Fertigung
umzusetzen - Ein schwieriges Unterfangen, welches viel Erfahrung erfordert.
Wo das Rechenmodell eine Splinekurve mit stetigen
Krümmungswechseln und kontinuierlichen Radienwechseln vorgibt, wird das
Schienenrohr über seine Länge in diskreten Radien gebogen. Statt
eines kontiniuerlichen Radienwechsels erfährt das Rohr auf der
Biegemaschine abgestufte Radienübergänge. Wo die Kurve im Modell
durch 500 oder mehr Stützpunkte beschrieben wird, wird sie für die
Fertigung auf ein anwendbares Mass an Stützkoordinaten zurechtgestutzt.
Dieser Prozess ist sich derart vorzustellen, dass eine Kurve, deren Radius sich
stetig über die Laufmeter ändert, für die Fertigung in
Abschnitte mit konstanten Radien eingeteilt wird. Ändert sich zum Beispiel
der Radius von 40 auf 20 Meter, so wird diese Radienänderung auf der
Schiene durchaus innerhalb von drei bis fünf Radienabstufungen
vorgenommen. Abweichungen von der hochgenauen Splinekurve des Computermodells
sind die Folge. Die Erstellung der Fertigungsanweisungen erfordert daher viel
Erfahrung, um selbst für Hochgeschwindigkeitsachterbahnen fern der 100
Stundenkilometer "weiche" Kurvenzüge zu gestalten. |
|
|
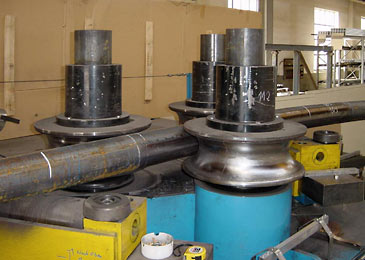 |
Kaltumformung der Stahlrohre auf der
Walzenstation im Werk von Gerstlauer |
Die typische Schienenfertigung besteht aus den folgenden
Schritten: Dem Biegen der Lauf- und Trägerrohre folgt ihre relative
Ausrichtung zueinander sowie die Anbringung der Querriegel auf
überdimensionalen, speziell für jede Schiene neu eingerichteten Lehrensystemen . Anschließend werden die Schienensegmente
abgeschweißt. Im vorletzten Schritt wird die Stossanpassung vorgenommen:
Damit die Schienen vom Werk zur Baustelle transportiert werden können,
müssen Container- oder LKW-Masse eingehalten werden. Je nach Krümmung
der Segmente sind Längen von sieben bis zwölf Meter die Regel. Die
Schienensegmente werden im Werk mit einem Stoß ausgestattet, so dass Sie
auf der Baustelle miteiander an dieser Fügestelle verschraubt werden
können. Vor der Auslieferung wird die Oberfläche der Schienen
gesandstrahlt, grundiert und lackiert. Neben der für den Kunden
individuellen Farbgebung, mit der sich jede Achterbahnschiene auszeichnet,
dient die Farbe vorwiegend als Korrosionsschutz.
Im Detail gestaltet sich der Fertigungsvorgang wie folgt:
Zuerst werden die Schienenrohre durch hohe Druckkräfte plastisch
umgeformt. Das gerade, maximal 14 Meter lange nahtlose Rohr erhält in
mehreren Umformschritten seine spätere, dreidimensionale Kurvenform, die
dem Computermodell nahekommt. Je nach Schienentyp - ob Zwei, Drei- oder
Viergurtschiene - werden die gebogenen Rohre im zweiten Arbeitsschritt mittels
Querriegeln miteinander verbunden. Dabei werden die Rohre auf ein
provisorisches, für jede Schiene jeweils neu einzurichtendes bzw.
anzufertigendes Gestell angepasst. Die Rohre werden solange gedreht, gewendet
und ausgerichtet, bis die vorgegebene Schienengeometrie auf der
Fertigungszeichnung erreicht ist und die Spurtreue eingehalten wird.
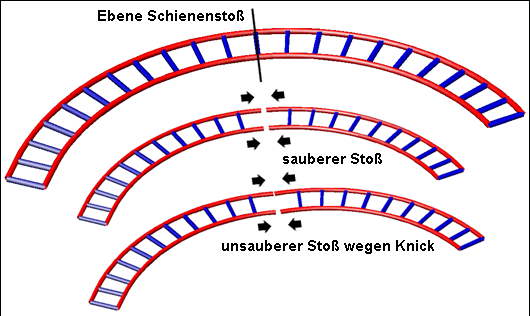 |
Schienenstoß visualisiert am
typischen Zweigurt |
Anschließend werden die Querriegel geheftet. Dieser
Vorgang wird mit den gleichen Werkzeugen durchgeführt wie das
anschließende Schweißen, jedoch wird die Schienenkonstruktion
vorläufig nur durch kleine Schweißpunkte zusammengehalten. Die
Belastungen eines Zug hält eine derart geheftete Schiene nicht aus, doch
kann das tonnenschwere Konstrukt mittels eines Kranes von der Lehre gehoben und
an einem anderen Ort abgeschweißt werden.
Dazu werden die Fügebereiche der Bauteile über
ihre Schmelztemperatur erhitzt. Gleichzeitig wird ein
Schweißzusatzwerkstoff in Form eines Drahtes geschmolzen und fließt
in die Verbindungsfuge. Nach dem Erstarrungsvorgang ergibt sich die
Schweißnaht, welche sich vom Grundwerkstoff der Stahlrohre praktisch
nicht unterscheidet und nahezu die gleichen Belastungen aushält wie der
Stahl der Schiene.
Im letzten Schritt erfolgt die Stoßanpassung. Die
fertig geschweißten Schienenelemente sind länger als ihre
endgültig geforderte Geometrie. Sie werden zueinander angepasst, so dass
in der Stoßebene ein sauberer Übergang von einem zum anderen
Fahrrohr gewährleistet ist. Anschließend werden an den beiden
Aussenseiten die beiden letzten Querriegel eingeschweisst, welche den
Stoß bilden. Am Aufbauort werden die Schienensegmente an diesen
Passstellen mit hochfesten Schrauben miteinander verbunden.
Während des Fertigungsprozesses wird ständig die
Spur der Schiene geprüft. Dabei ist viel Know How gefragt, denn
während des Schweißprozesses bewirkt die hohe Wärmeeinbringung,
dass sich die Rohre beim Abkühlen verziehen. Schon Abweichungen von
wenigen Millimeter können bei hohen G-Lasten zu spürbaren
Rüttlern des Zuges führen.
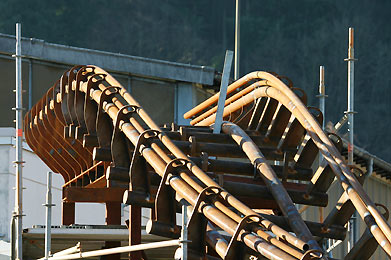 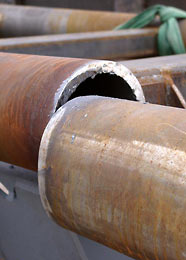 |
Im Freien werden die Schienen auf
Gerüsten montiert um u.a. die Schienenstöße zu
kontrollieren |
Daher setzen qualitätsbewusste Fertiger die Schienen
von komplexen Fahrfiguren wie Loopings oder engen Steilkurven auf dem
Werksgelände provisorisch zusammen oder schieben das später
verwendete Fahrzeug sogar über die Schiene. Zwischen den Schienenrohren
muss ein glatter Übergang herrschen, jede Unstetigkeit in Form eines
Knicks ist unerwünscht. Wurde beim Heften ungenau gearbeitet, so
fällt dies beim testweisen Zusammensetzen auf und ist korrigierbar. Nach
finaler Schweißung ist eine Korrektur nicht mehr möglich. Entweder
muss der unsaubere Stoß hingenommen werden oder die Schiene ist Ausschuss
und landet beim Altmetall.
Jedoch ist diese Art der Qualitätssicherung sehr
aufwändig und bedarf eines enormen Aufwandes. Die über zehn Meter
langen, tonnenschweren Schienensegmente, die am späteren Einsatzort in 30
oder mehr Meter Höhe angebracht sind, können nicht einfach per Hand
zusammengefügt werden. Dazu wird schweres Krangerät, aufwendige
Gestelle, sowie viel Zeit und Muskelkraft benötigt. Entsprechend
verzichten einige Hersteller auf derart aufwändige Prüfmethoden und
können damit ihre Bahnen weitaus günstiger am Markt anbieten.
Letztendlich kann die Schienenqualität unter den
Kosteneinsparungen leiden. Bei Schienenpreisen von etwa 20.000 Euro für
zehn Meter Strecke will jedes Einsparpotential wohlkalkuliert sein. Allein die
Schiene einer 1000 Meter langen Achterbahn schlägt mit rund zwei Millionen
Euro zu Buche - Stützen und der Aufwand für die
computerunterstützte Auslegung nicht inbegriffen.
Fallen potentielle, unsaubere Stöße erst auf der
Baustelle auf, kann in Zeiten von just-in-time-gelieferten Achterbahnteilen nur
noch der Einbau erfolgen und anschließend versucht werden, beim finalen
Schleifen der Schienenstöße den Fehler auszugleichen. Trotzdem ist
diese Flicklösung dem Fahrkomfort nicht förderlich und die
Fahrgäste werden mitunter unsanft in Sitz und Bügel
gedrückt. |
|
|
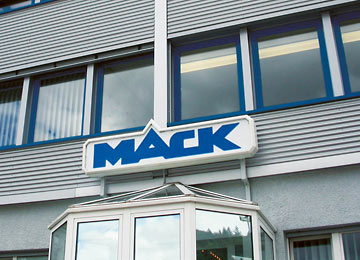 |
Bei Mack Rides in Waldkirch wurde die neue
Schienenfertigungsmethode entwickelt |
Die detaillierte Darstellung der einzelnen
Herstellungssschritte einer Achterbahnschiene lassen erkennen, dass eine hohe,
durchgehende Qualität bei der herkömmlichen Fertigungsmethode nur
durch aufwändige Kontrollmaßnahmen zu erreichen ist, die sehr viel
Zeit und Kosten in Anspruch nehmen. Die Firma Mack Rides hat sich dieses
Problems angenommen und setzt auf eine Rechnerunterstützung innerhalb der
Geometrieherstellung der Schiene. So wie der Computer bei der Auslegung der
Schiene nicht mehr wegzudenken ist, so kann er auch bei der Schienenfertigung
simultan zu den Fertigungsschritten die Geometrie der Schiene
überprüfen und damit für lupenreine Übergänge und
exakte Spurtreue sorgen. Das Ergebnis trägt den Namen
Nullebenenfertigung.
Entwickler des Fertigungsverfahrens ist der Mack
Rides Produktionsleiter Thomas Kern, mit seinem Projektteam, welches
sich aus den Personen Burger, Köbele, Sornik und
Hug zusammensetzt. Thomas Kern hat im Jahre 2002 seine Arbeit
beim traditionsreichen Familienbetrieb aufgenommen. Der in der Serienfertigung
groß gewordene Ingenieur hatte in vielen Bereichen eine rein handwerklich
ausgerichtete Firma vorgefunden - So auch im Bereich der Schienenfertigung.
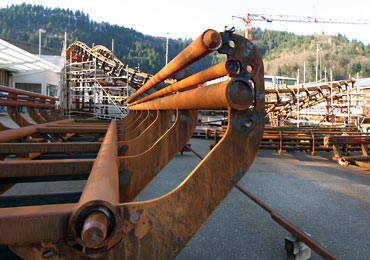 |
Schienenqualitätskontrolle nach der
herkömmlichen Methode für eine neue Wasserachterbahn von Mack
Rides |
"Wenn ich aus meinem Büro auf die große
Freifläche geschaut habe, wo die Arbeiter bei Wind und Wetter auf riesigen
Gerüsten die gehefteten Schienen provisorisch aneinandersetzten, und das
vornehmlich noch im Winter für die Auslieferung im Frühjahr, baute
sich vor meinem geistigen Auge eine Vision auf, die derart aufwändige
Kontrollarbeiten nicht mehr benötigt", sagt Thomas Kern heute.
"Jedes Problem ist eine Aufgabe, und die galt es zu lösen".
Neben den zeitraubenden Arbeiten im Freien auf Gerüsten
von bis zu 20 Metern Höhe sah Thomas Kern bei dem
herkömmlichen Schienenfertigungsverfahren die Nachteile in den hohen
Rüstkosten des Arbeitsplatzes, langen Durchlaufzeiten und einer
schwierigen Qualitätssicherung.
Vor allem der Zeitaufwand, um die gehefteten Schienen auf
ihre Passgenauigkeit untereinander und zu den Stützen zu kontrollieren,
erschien ihm eindeutig zu hoch. Ein 350 Meter langer Schienenparcours eines
Powered Coaster benötigte intern rund fünf Monate, bis die
Schiene auslieferungsfähig war. In Zeiten, in denen die Bahnen für
die nächste Saison noch im Oktober oder selbst November des Vorjahres
bestellt werden, eine schwierige Ausgangssituation für den
mittelständischen Fertigungsbetrieb in Waldkirch. Während im Sommer
die Produktion lahmt, ist im Herbst und Winter die Kapazität vollends
ausgereizt. Im Hause Mack Rides wird im Vergleich zu anderen
Achterbahnbauern noch alles am eigenen Standort hergestellt - auf die Vergabe
der Schienenfertigung an externe Firmen wird nur ungern ausgewichen, allein den
eigenen hohen Qualitätsansprüchen wegen. |
|
 |
|
|
Aufwendig entsteht auf
dem Aussengelände von Mack Rides in Waldkirch eine neue Wasserachterbahn
für Spanien nach der herkömmlichen Methode |
|
Eine Fertigungsmethode, welche die Durchlaufzeit der Schiene
drastisch verkürzt, den Arbeitsaufwand gering hält und gleichzeitig
die eine durchgehend hohe Qualität liefert, war ein weitgestecktes Ziel,
letztendlich eine wahre Herausforderung: "Das Unmögliche hat seinen
besonderen Reiz", sagt Thomas Kern, als er an die ersten Tage und Wochen
der Ideenfindung für das neue hauseigene Schienenfertigungssystem
zurückdenkt. "Wenn wir dann noch die Kosten pro Schienenmeter gering
halten können, hat dies sogar einen Mehrwert für den Kunden." Doch
was verbirgt sich hinter dem Begriff der Nullebenenfertigung? Coastersandmore
konnte exklusiv einen Blick auf das rechnerunterstütze Fertigungssystem
werfen. |
|
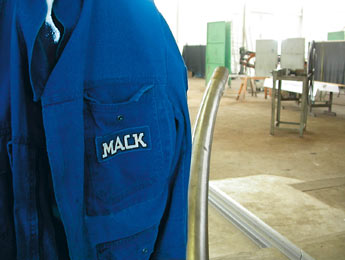 |
Das Geheimnis der Nullebene wird
gelüftet... |
Die "Nullebene" bildet den Mittelpunkt des Mack'schen
Fertigungsverfahrens. Sie lässt sich auf jedem Fertigungsplatz eingelassen
im Hallenboden finden. Dort befinden sich mehrere Stahlplanken, welche in ihrer
Gesamtheit die Fertigungsebene bilden. Auf der Nullebene sind bis zu fünf
sogenannte Lineale angebracht, die mittels Schnellspannern beliebig in
Höhe und Winkellage in drei Achsrichtungen verstellt werden können.
Die Lineale sind gleichzeitig die temporären Halterungen für die
Schienenrohre. Mittels eines einfach handhabbaren Stecksystems sind sie
beliebig auf der Nullebene positionierbar. Zusätzlich findet sich etwas
abseits ein großes Stativ mit einem Laser
Tracker System , welches als
Sprachrohr zwischen dem Fertigungsplatz auf der Nullebene in der Halle und
seinem virtuellen Abbild im Computer fungiert.
Der Laser Tracker fokussiert ständig eine
reflektierende Stahlkugel, die im Raum von einem Mitarbeiter bewegt wird. Die
genaue Position von Bauteilen über der Nullebene ist somit sehr einfach
mit einer Genauigkeit von wenigen Hunderstel Millimetern vom Rechnersystem
erfassbar und kann direkt in der virtuellen Realität auf dem
Computermonitor angezeigt werden.
Die Mack'sche Nullebenenfertigung macht aus der komplexen
Schienenfertigung ein überschaubares und simples Baukastensystem. Das zu
fertigende Schienenelement wird aus dem globalen Koordinatensystem des
virtuellen Tracks genommen und vom Rechner auf dem lokalen Koordinatensystem
der Nullebene im virtuellen Raum optimal für die Fertigung platziert. Ein
identisches, reales Abbild der Nullebene findet der Arbeiter auf dem
Hallenboden wieder. Somit gibt der Rechner eine "dreidimensionale Schablone"
vor, die oberhalb der realen Nullebene in der Werkhalle vom Bediener
einzuhalten ist. Die Arbeitsweise verbindet Fertigung und
Qualitätssicherung in einem. Maßwerkzeuge oder aufwändige,
für jede Schiene anzupassende Lehrenschablonen werden nicht
benötigt.
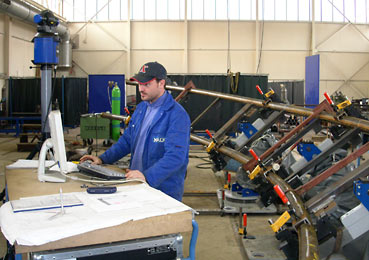 |
Mensch und Computer vereint am
Arbeitsplatz der Nullebenenfertigung - im Hintergrund der Laser
Tracker |
Die Prozedur der Schienenfertigung im Hause Mack
Rides gestaltet sich äußerst einfach. Die nach den Biegedaten
gebogenen Schienenrohre werden auf den Linealen eingepasst. Mittels
Schnellverschlüssen werden die Rohre festgeklemmt. Die genaue Lage der
Lineale und der Rohre im Raum über der Nullebene wird vom virtuellen
Soll-3D-Modell der Schiene vorgegeben. Egal in welchem Winkel und Höhe die
Schiene später in der Achterbahn verschraubt wird, die Fertigungsposition
der Schiene liegt in einem Meter über dem Hallenboden. Die Einpassung
geschieht simultan zur Messung von wenigen Punkten auf den Schienenrohren durch
das Laser Tracker System. Dazu wird die Kugel einfach auf den Messpunkten
platziert und automatisch vom Laser erfasst. Jeder Messpunkt ist
sekundenschnell im Raum über der Nullebene ermittelt und der Mack
Rides Arbeiter erhält direkt Rückmeldung, ob das real
positionierte Schienenrohr mit der virtuellen Vorgabe aus dem Computer
übereinstimmt. Jede Abweichung wird sofort vom Rechnersystem festgestellt
und kann direkt korrigiert werden.
Als besonderen Clou speichert das System für jede
Schiene den anschließend gefertigten Ist-Zustand bei Heftung der
Bauteile. Dadurch, dass die gefertigte Geometrie jedes Schienensegmentes dem
System bekannt ist, liegt für die sich in Fahrtrichtung
anschließende Schiene ein virtueller Schienenstoß im Rechner vor,
den der Arbeiter nur noch einzuhalten hat. Das Setzen jedes
Schienenstoßes erfolgt praktisch in der virtuellen Realität, da
keine Schienen mehr im Werk aneinander gepasst werden müssen. Selbst
potentielle Abweichungen der real gefertigten Schiene von der Vorgabe
können somit wieder ausgeglichen werden. Nach erfolgter Ausrichtung und
Einpassung auf den Linealen werden die Querriegel, Rohre und
Stützenköpfe geheftet.
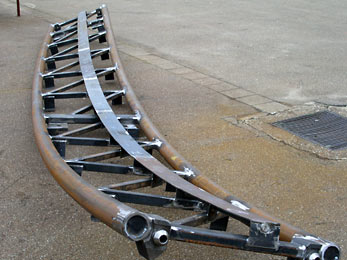 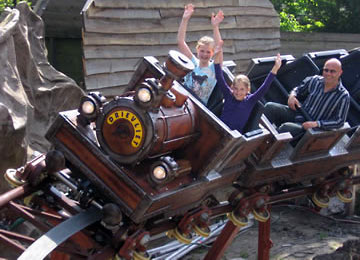 |
Links: Fertige Powered Coaster Schiene
für Drievliet - rechts: Die Anlage in Betrieb |
Die Geschwindigkeit der Nullebenenfertigung ist enorm: In
kürzester Zeit können die Lineale für jede beliebige
Schienenform eingestellt und die Schienengeometrie mit abschließender
Heftung vorgenommen werden. Die gleichzeitige virtuelle Realität des
Computermodells interagiert mit der realen Welt in der Werkhalle automatisch
mittels des Laser Trackers. Es folgt ein derart hochgenaues Abbild der
virtuellen Schiene aus dem Rechner, dass nach dem anschließenden
Schweißen die Schienestöße um Hunderstel Millimeter genau
aneinanderpassen. Selbst der Schweißverzug der Schiene durch die hohe
Wärmeeinbringung beim anschliessenden Schweißen wird vom System
einkalkuliert. Stück für Stück entsteht mit jeder gefertigten
Schiene ein Abbild der Bahn im Rechner, ohne dass die Schienenelemente jemals
im Werk abschnittsweise zur Kontrolle zusammengesetzt werden.
Die Maß- und Passgenauigkeit der Schienen
untereinandern und zu ihren Stützenanschlüsslen wird nur noch mittels
des virtuellen Fertigungsabbildes kontrolliert. Zusammengeschraubt werden die
Schienen erst auf der Baustelle im Park und trotzdem weiß die Mack
Rides Crew schon bei der Fertigung, dass die Schienen haargenau aneinander
und auf die Fundamente passen. Was vorher durch den Zusammenbau auf dem
Werksgelände von den Mitarbeitern bei Wind und Wetter aufwändig
angepasst wurde, absolviert der Computer simultan zur eigentlichen Platzierung
der Rohre und Querriegel auf den Linealen. Die Qualitätssichung läuft
von selbst in der virtuellen Realität ab, ohne dass ein Mitarbeiter
anschließend zu aufwändigen Messverfahren greifen müsste. Eine
revolutionäre Idee, die neben ihrer hohen Qualität der Schiene und
Stöße Kosten spart, dem Arbeiter einen komfortablen Arbeitsplatz zur
Verfügung stellt und die Fertigung der Schiene um nahezu den Faktor 2
verkürzt: Waren es früher noch fast fünf Monate, die man im Werk
für 350 Meter Schiene benötigte, sind es nun keine zehn Wochen
mehr.
"Zu Beginn waren die Mitarbeiter in der Fertigung sehr
skeptisch", sagt Thomas Kern, "doch als die ersten Schienen provisorisch
am Kran hingen und miteinander verbunden wurden, waren sie von der hohen
Passgenauigkeit des Stoßes beeindruckt. Nun sind alle von der
Nullebenenfertigung regelrecht infiziert." Das Ergebnis konnte zum ersten Male
beim Powered Coaster im niederländischen Drievliet bestaunt
werden kann. "Beim Aufbau hat sich gezeigt, dass beim Dynamite Express wirklich
alle Schienen perfekt zusammenpassen. Und durch die Nullebene konnten die
beiden Umschwünge deutlich rasanter ausfallen als bisher. Dabei sind die
Laufruhe und der Fahrkomfort noch einmal spürbar besser geworden",
ergänzt Kern.
Text: Coastersandmore - jp, Bilder: Coastersandmore,
Gerstlauer (1), goldorange (3), Mack Rides (5) |
|
|
|